Powerex Scroll Base Mounted Compressor System
Oilless unit with dynamically balanced air end for vibration-free operation.
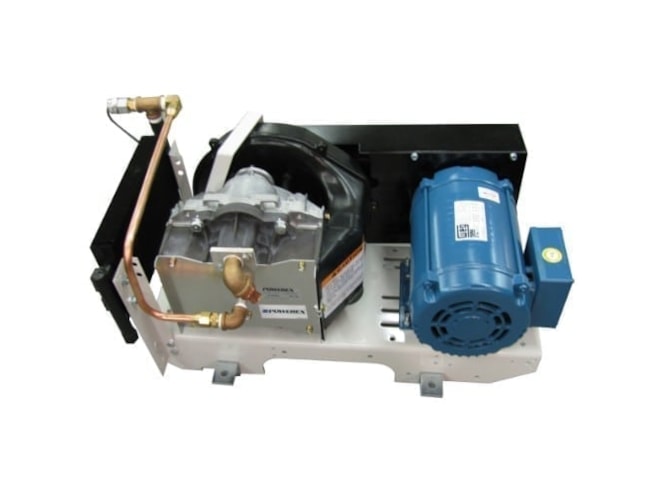
Overview
Features
- 115 psi standard maximum pressure (145psig high pressure option available)
- 34° F to 104° F (1° C to 40° C) operating temperature at inlet
- 0.5in outlet air connection
- ASME safety valve factory set and sealed overpressure protection
- 2 to 3 V belt drive
- Grease filled bearings
- Manufactured in ISO 9001:2015 certified facilities
- Starters are shipped loose for 7.5 and 10 HP options
Description
The Powerex Scroll Base Mounted Compressor System is based on the theory of scroll compression. A scroll is a free standing, intricate spiral bounded on one side by a solid, flat plane or base. A scroll set, the basic compression element of a scroll compressor, is made up of two identical spirals that form right and left hand parts. One of these scroll components is indexed or phased 180° with respect to the other so the scrolls can mesh. Crescent-shaped gas pockets are formed and bounded by the spirals and the base plate of both scrolls. As the moving scroll is orbited around the fixed scroll, the pockets formed by the meshed scrolls follow the spiral toward the center and diminish in size. The moving scroll is prevented from rotating during this process so the 180° phase relationship of the scrolls is maintained. The compressor’s inlet is at the outer boundary of the scrolls. The compressed gas is discharged through the outlet at the center of the fixed scroll so no valves are needed.
The tip seal on the scroll compressor is self-lubricated and allows the unit to operate efficiently without oil. On standard pressure units, the tip seal should be replaced every 10,000 hours of operation. On high pressure units, the tip seal should be replaced every 5,000 hours. The system's rotary design permits a continuous 100% duty cycle. No oil separation, oil filtration, or inlet valves are required on the scroll unit.
Documents
Reviews
Reviews
-
Working really well
Reviewed on 5/17/2021So far its working really well. It's driving the front end of the system. It is relatively quiet which is a staff satisfier.- Jacob -
Powerex Is The Way To Go
Reviewed on 10/30/2019We have made the switch to this Powerex unit for our remediation trailers and they have been great. We will spec them for our next two projects because of their reliability and performance and we will always deal with the guys at Compressor World. Their knowledge and customer support is top notch and we appreciate doing business with them. Will always recommend people to Compressor World.- Rick -
Very Easy to Deal With
Reviewed on 7/30/2019Dealing with Andy in Sales was great. He was very responsive in getting us a quote and all the information that our customer required. The equipment was at our customer's location when promised and we have a happy customer. Compressor World will surely be on our vendor list for future projects- Joe -
Perfect for Our Operation
Reviewed on 6/21/2019Being located in an office building, we face many restrictions in terms of what type of machines we can have in our design shop. This Powerex machine meets multiple requirements by being oil-less and quiet; perfect for our CAD machine and 3D printer. We found the Compressor World website to be very informative and then when we called in to make the purchase, the staff was friendly and made the process very easy. Great experience.- Paige -
Great Pricing
Reviewed on 4/1/2019This is our 3rd purchase with Compressor World (tank, dryer, and now scroll pump) and the pricing on the replacement pump was the best around. It is a great website that covers all of our needs and we will continue to do business with them.- Eric
Need Help? Call an expert at 1-866-778-6572
We're open 8:00 am to 5:00 pm ET